Best siding for hurricane prone areas – Best siding for hurricane-prone areas? It’s a question homeowners in vulnerable regions grapple with constantly. Choosing the right siding isn’t just about aesthetics; it’s about safeguarding your home and family from the brutal force of nature. We’re diving deep into the materials, installation, and long-term considerations to help you make an informed decision that protects your investment for years to come.
This guide covers everything from impact-resistant fiber cement to the wind-defying properties of metal siding, helping you navigate the complexities of hurricane preparedness.
This isn’t just about picking a pretty facade; it’s about selecting siding that can withstand the relentless battering of high winds, flying debris, and torrential rain. We’ll explore the pros and cons of various materials, examining their durability, maintenance needs, and overall cost-effectiveness. We’ll also touch on crucial installation techniques and building codes to ensure your siding offers maximum protection.
Get ready to weather the storm with confidence!
Types of Siding Materials
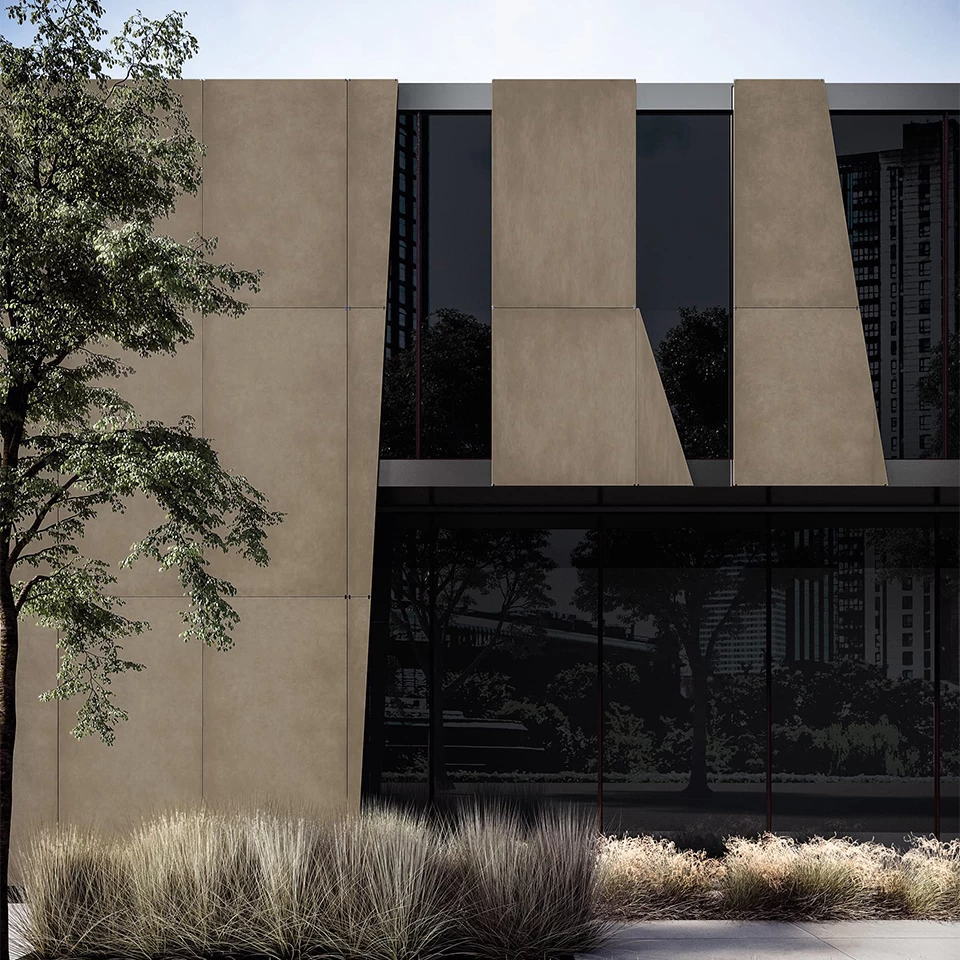
Choosing the right siding for your home in a hurricane-prone area is crucial for protecting your investment and ensuring your family’s safety. The right material can withstand high winds, heavy rain, and flying debris, minimizing damage and reducing repair costs. Several siding options offer varying degrees of protection and longevity. Understanding their strengths and weaknesses is key to making an informed decision.
Fiber Cement Siding
Fiber cement siding is a popular choice for hurricane-prone areas due to its exceptional durability and resistance to damage. This composite material, made from cement, cellulose fibers, and sand, is incredibly strong and fire-resistant. It’s also resistant to rot, insects, and moisture. However, fiber cement siding is heavier than other options, requiring more robust installation, and it’s more expensive upfront.
It can also be brittle and prone to cracking if improperly installed. Furthermore, it requires more maintenance than vinyl siding.
Vinyl Siding
Vinyl siding is a cost-effective and readily available option, known for its low maintenance requirements. It comes in a wide variety of colors and styles, offering aesthetic versatility. While generally resistant to moisture and rot, vinyl siding’s impact resistance is lower compared to fiber cement or metal. In high winds, it can be damaged, and its susceptibility to warping or fading in intense sunlight should be considered.
Its lifespan is also shorter than fiber cement or metal siding.
Metal Siding
Metal siding, typically made of aluminum or steel, boasts superior impact and wind resistance, making it an excellent choice for hurricane-prone regions. It’s exceptionally durable and long-lasting, resisting damage from high winds, hail, and flying debris. Metal siding is also fire-resistant and low-maintenance. However, it can be more expensive than vinyl or even fiber cement, and its susceptibility to dents and scratches should be considered.
Additionally, it can be noisy during heavy rain or hail.
Engineered Wood Siding
Engineered wood siding, often treated with preservatives to resist rot and insects, presents a compromise between the natural look of wood and the durability needed in hurricane-prone areas. It offers a good balance of aesthetics and performance, but its resistance to wind and water damage is lower than metal or fiber cement. Proper installation and regular maintenance are crucial to ensure its longevity.
Compared to other options, engineered wood siding generally has a shorter lifespan and may require more frequent maintenance.
Comparison of Siding Materials
The following table summarizes the key characteristics of each siding type:
Siding Material | Impact Resistance | Wind Resistance | Water Resistance | Maintenance |
---|---|---|---|---|
Fiber Cement | High | High | High | Moderate |
Vinyl | Moderate | Moderate | High | Low |
Metal | High | High | High | Low |
Engineered Wood | Moderate | Moderate | Moderate | Moderate |
Lifespan and Warranty Information
Lifespan and warranty information vary significantly depending on the manufacturer, material quality, and installation. However, general estimates include: Fiber cement siding typically lasts 50 years or more, with warranties often covering 30-50 years. Vinyl siding usually lasts 20-30 years, with warranties ranging from 10-25 years. Metal siding can last 50 years or more, with warranties often exceeding 30 years.
Engineered wood siding typically lasts 20-30 years, with warranties often around 10-20 years. It’s crucial to check individual manufacturer specifications for specific warranty details.
Impact Resistance and Wind Load Considerations

Choosing the right siding for a hurricane-prone area isn’t just about aesthetics; it’s about safeguarding your home from the brutal forces of nature. Impact resistance and wind load capacity are critical factors that determine a siding’s ability to withstand high winds, flying debris, and the overall pressure exerted during a hurricane. The wrong choice can lead to significant damage, costly repairs, and even compromise the structural integrity of your house.High winds and airborne debris pose significant threats to homes in hurricane-prone regions.
The impact resistance of siding materials directly correlates to their ability to withstand these impacts without cracking, denting, or failing. Materials like fiber cement and vinyl offer varying levels of impact resistance, while others, such as wood, are inherently more vulnerable. Similarly, wind load capacity, which measures a material’s ability to resist the force of wind pressure, is crucial.
A siding with high wind load capacity is less likely to be ripped away from the house during a storm. The interaction between these two factors—impact resistance and wind load capacity—determines the overall resilience of the siding system.
Impact Resistance of Different Siding Materials, Best siding for hurricane prone areas
The ability of siding to resist impact from flying debris is paramount in hurricane zones. Fiber cement siding, known for its strength and durability, generally exhibits superior impact resistance compared to vinyl or aluminum siding. While vinyl siding offers decent performance, it can be susceptible to cracking or denting from forceful impacts. Wood siding, unless exceptionally thick and treated, is relatively vulnerable to damage from windborne debris.
Metal siding, particularly steel, offers good impact resistance but can dent under extreme force. The choice of material should be carefully considered based on the severity of expected impacts in the specific location. For example, a region known for frequent hailstorms would benefit from a siding with high impact resistance, such as fiber cement.
Role of Proper Installation in Maximizing Wind Resistance
Proper installation is as crucial as material selection in ensuring the wind resistance of your siding. Neglecting proper installation techniques can severely compromise even the most impact-resistant siding. For instance, ensuring adequate fastening—using the correct number and type of nails or screws at appropriate intervals—is critical. Improper fastening can lead to siding being ripped off during high winds.
Furthermore, maintaining proper overlaps between siding panels is essential to prevent wind from penetrating the siding system. Finally, ensuring a proper seal around windows and doors is vital to prevent wind from entering the house and causing damage. These steps are not optional, but critical components of a hurricane-resistant siding system.
Visual Representation of Wind Load on Different Siding Types
Imagine three identical houses, each clad with a different type of siding: fiber cement, vinyl, and wood. A strong wind, represented by arrows pushing against each house with equal force, is simulated. The fiber cement house shows minimal deformation; the arrows barely affect the siding. The vinyl house shows some bowing and slight flexing under the wind pressure.
The wood house, however, shows significant bowing and potential for cracking or detachment, with the arrows visibly causing greater deformation. This visualization illustrates how different siding materials react to the same wind load, highlighting the superior wind resistance of fiber cement compared to vinyl and wood in this scenario. This example underscores the importance of choosing a material with high wind load capacity for hurricane-prone areas.
Water Resistance and Moisture Management
Protecting your home’s structure from water damage is paramount, especially in hurricane-prone areas where intense rainfall and potential flooding are significant threats. The choice of siding material and its proper installation directly impact the building’s longevity and resistance to water intrusion. Understanding the water absorption properties of various siding options and employing effective moisture management strategies are crucial for ensuring long-term structural integrity.Proper flashing and sealing are essential components of a robust water-resistant siding system.
These techniques act as barriers, preventing water from penetrating the building envelope and causing damage to the underlying sheathing, insulation, and framing. Different siding materials require specific flashing and sealing methods to achieve optimal performance. Failing to address these aspects can lead to costly repairs down the line, including mold growth and structural weakening.
Flashing and Sealing Techniques
Effective flashing and sealing prevent water from seeping behind the siding. Flashing, typically made of metal or synthetic materials, is installed at critical areas such as window and door frames, rooflines, and other transitions in the building envelope. It directs water away from these vulnerable points. Sealants, such as caulking or specialized tapes, create a watertight seal around penetrations and joints in the siding system.
For instance, around windows, a continuous layer of flashing should be installed under the window trim, extending several inches beyond the window frame. Then, the siding is carefully installed over the flashing, ensuring a proper overlap. All gaps and joints between siding pieces and around window and door frames should be filled with high-quality, weather-resistant sealant. Different sealants have varying properties; some are better suited for extreme temperatures or UV exposure than others.
Choosing the best siding for hurricane-prone areas requires careful consideration of impact resistance and durability. To ensure your choice complements your home’s aesthetic, remember to check out this helpful guide on how to choose the right siding for your home’s style before making a final decision. Ultimately, the best siding will offer both superior protection from extreme weather and a beautiful finish that enhances your property’s curb appeal.
The choice of sealant should match the climate and siding material.
Water Absorption and Mold Resistance of Siding Materials
The water absorption rate of siding materials significantly influences their susceptibility to damage and mold growth. Materials with low water absorption, like vinyl and fiber cement, generally perform better in humid or rainy climates. Vinyl siding, for example, is known for its virtually zero water absorption, making it highly resistant to moisture damage. However, even low-absorption materials can be compromised if not properly installed and sealed.
Conversely, wood siding, while aesthetically pleasing, has a higher water absorption rate and is more prone to rot and mildew if not treated properly with water-resistant coatings and maintained regularly. For instance, cedar siding, while beautiful, requires periodic sealing to maintain its water resistance. Fiber cement siding, though more expensive, offers a good balance of durability, water resistance, and aesthetic appeal.
Its lower water absorption rate makes it a popular choice for hurricane-prone areas. A comparison of water absorption rates across different siding types reveals significant differences; therefore, careful consideration is necessary when choosing siding for hurricane-prone regions.
Installation and Maintenance: Best Siding For Hurricane Prone Areas
Proper installation and regular maintenance are crucial for maximizing the lifespan and performance of your hurricane-resistant siding, ensuring your home remains protected for years to come. Neglecting these aspects can lead to premature damage, costly repairs, and compromised structural integrity, especially in areas prone to severe weather. This section details the installation process for two common siding types and Artikels long-term maintenance requirements.
Siding Installation Processes
The installation process for different siding materials varies significantly. Understanding these nuances is vital for achieving a robust and weatherproof exterior. Improper installation can negate the benefits of even the most durable siding.
Choosing the right siding is crucial in hurricane-prone areas, with impact-resistant materials being paramount. However, even the toughest siding can suffer damage, necessitating repairs. Knowing how to tackle these issues is key, which is why understanding common problems and solutions is essential; check out this helpful guide on DIY siding repair: common problems and solutions for some great tips.
Ultimately, selecting durable siding and knowing how to maintain it are vital for protecting your home from severe weather.
- Fiber Cement Siding Installation: Fiber cement siding offers excellent durability and impact resistance. Installation typically involves the following steps:
- Prepare the wall surface: Ensure the wall is clean, dry, and free from any loose debris or damaged areas. This might involve patching holes or repairing damaged sheathing.
- Install sheathing and house wrap: This layer provides additional protection against moisture and wind. Ensure proper overlap and sealing of the house wrap to prevent water intrusion.
- Install starter strips: These strips provide a level base for the first row of siding.
- Install siding panels: Begin at the bottom and work your way up, ensuring proper alignment and overlap. Use appropriate fasteners for secure attachment.
- Install trim and finishing pieces: This step completes the look and seals any gaps.
- Vinyl Siding Installation: Vinyl siding is a popular choice for its affordability and ease of installation. The process is generally as follows:
- Prepare the wall surface: Similar to fiber cement, clean and prepare the wall surface for a smooth installation.
- Install J-channel and starter strips: These guide the installation of the vinyl panels.
- Install siding panels: Vinyl panels typically interlock, making installation relatively straightforward. Begin at one corner and work your way across the wall.
- Install finishing pieces: Corner trim, J-channel, and other finishing pieces are installed to complete the installation and provide a neat, finished look.
- Caulk and seal: Caulk around windows, doors, and other areas where gaps may exist to prevent water intrusion.
Long-Term Siding Maintenance
Regular maintenance is key to prolonging the life of your siding and maintaining its protective qualities. The specific needs vary depending on the siding material.
- Cleaning: Regular cleaning helps remove dirt, debris, and mildew, preventing damage and maintaining the appearance of your siding. For most types, a pressure washer can be effective, but avoid using excessive pressure which can damage the siding. For fiber cement, use a mild detergent and water solution. For vinyl, simply hose it down.
- Repair: Promptly repair any damaged sections of siding to prevent further damage and water intrusion. This may involve replacing individual panels or sections, depending on the extent of the damage. Always use matching materials for repairs.
- Replacement: Eventually, siding will need replacement due to age, damage, or wear and tear. The lifespan varies greatly by material and exposure. Regular inspection will help identify when replacement is necessary.
Estimated 20-Year Cost Comparison
The following table provides estimated costs for installation and maintenance over a 20-year period. These figures are averages and can vary based on factors such as labor costs, material prices, and the size of the house. These estimates are based on a hypothetical 2000 square foot home and may vary depending on location and specific project requirements.
Siding Material | Installation Cost | Annual Maintenance Cost | Total 20-Year Cost |
---|---|---|---|
Fiber Cement | $10,000 – $20,000 | $100 – $300 | $12,000 – $26,000 |
Vinyl | $5,000 – $15,000 | $50 – $150 | $6,000 – $18,000 |
Wood (Cedar) | $15,000 – $30,000 | $200 – $500 | $19,000 – $30,000 |
Aluminum | $7,000 – $17,000 | $75 – $225 | $8,500 – $21,500 |
Building Codes and Regulations
Navigating the complex world of building codes in hurricane-prone areas is crucial for ensuring your home’s safety and longevity. These regulations aren’t just suggestions; they’re legally mandated guidelines designed to protect lives and property against the destructive forces of nature. Understanding these codes is paramount when choosing and installing siding.Building codes in hurricane-prone regions, such as those defined by the International Building Code (IBC) and supplemented by local ordinances, dictate stringent requirements for exterior cladding, including siding.
These regulations often specify minimum wind resistance ratings, impact resistance levels, and acceptable installation methods to withstand high winds, flying debris, and heavy rainfall associated with hurricanes. Failure to comply can result in building permit denial, insurance complications, and, most importantly, compromised structural integrity during a storm.
Wind Load Requirements and Impact Resistance Ratings
Wind load requirements define the amount of force a structure must withstand during high winds. These are typically expressed in pounds per square foot (psf) and vary depending on the geographic location, the building’s design, and its height. Impact resistance ratings, often expressed using the Florida Building Code’s (FBC) impact-resistance testing standards, measure a material’s ability to withstand impacts from flying debris.
For instance, a higher wind load requirement might necessitate the use of stronger, heavier siding materials, while a higher impact resistance rating would necessitate materials that can better withstand the impact of debris during a hurricane. Compliance with these ratings ensures that the siding can effectively resist the forces of a hurricane, preventing damage and protecting the underlying structure.
For example, a home built to withstand 150 mph winds using high-impact resistant siding would likely fare better than a home with lower-rated materials during a Category 3 hurricane.
Specific Code Examples and Their Impact on Siding Selection
Many coastal areas have adopted stringent building codes, particularly concerning siding. The Florida Building Code, for example, is a widely referenced model code that includes detailed specifications for hurricane-resistant construction. These codes often mandate the use of specific materials, such as impact-resistant vinyl siding or fiber cement siding that meet designated impact resistance ratings. Additionally, codes specify requirements for proper fastening, ensuring that the siding is securely attached to the underlying sheathing to prevent it from being torn away by high winds.
Failure to comply with these fastening requirements could result in significant damage to the home’s exterior during a hurricane. For instance, a home built in accordance with the FBC, using appropriately fastened impact-resistant siding, would be significantly better protected from damage than a home built without consideration for these specific requirements.
Enforcement and Inspection Processes
Building inspectors play a vital role in ensuring compliance with building codes. They conduct inspections at various stages of construction, including the installation of siding, to verify that the materials and installation methods meet the required standards. This process helps to ensure that homes are built to withstand hurricane-force winds and protect occupants. Failure to pass inspections can lead to delays in the construction process and potentially require costly modifications to bring the structure into compliance.
A rigorous inspection process, therefore, acts as a safeguard, ensuring that the building’s structural integrity is not compromised, ultimately safeguarding lives and property.
Sustainability and Environmental Impact

Choosing sustainable siding isn’t just about aesthetics; it’s a crucial step towards responsible homeownership, especially in hurricane-prone areas where replacements might be more frequent. The environmental footprint of siding extends far beyond its initial purchase, encompassing manufacturing, transportation, installation, maintenance, and ultimately, disposal. Understanding these impacts is key to making an informed decision.The environmental impact of different siding materials varies significantly throughout their lifecycle.
Manufacturing processes consume energy and resources, often generating waste and emissions. Transportation adds to the carbon footprint, while the material’s lifespan and eventual disposal further contribute to the overall environmental impact. For instance, vinyl siding, while often affordable, relies on petroleum-based plastics, resulting in a larger carbon footprint compared to more sustainable alternatives. Conversely, fiber cement siding, though initially more expensive, offers a longer lifespan and potentially lower long-term environmental impact.
Life Cycle Assessment of Siding Materials
A comprehensive life cycle assessment (LCA) considers all stages of a product’s life, from raw material extraction to end-of-life management. LCAs provide a holistic view of a material’s environmental impact, allowing for a more accurate comparison between different siding options. For example, a detailed LCA of wood siding would factor in deforestation rates, energy used in processing and transportation, and the potential for carbon sequestration.
Similarly, an LCA for metal siding would assess the energy consumption during metal production, the use of protective coatings, and the recyclability of the material at the end of its life. While comprehensive LCAs can be complex, they provide valuable data for consumers seeking environmentally conscious choices.
Recycled and Sustainable Siding Options
The availability of recycled or sustainable siding options is growing, offering homeowners environmentally friendly alternatives. Recycled plastic siding, for example, utilizes post-consumer plastic waste, reducing landfill burden and lowering the demand for virgin materials. Similarly, some manufacturers are incorporating recycled content into fiber cement and composite siding, further minimizing the environmental impact. Moreover, sustainably harvested wood siding, certified by organizations like the Forest Stewardship Council (FSC), ensures responsible forestry practices.
These options are becoming increasingly popular as consumers become more aware of the environmental implications of their choices.
Energy Efficiency and Siding Materials
Different siding materials offer varying levels of energy efficiency, influencing a home’s heating and cooling needs. High-performance siding materials, such as insulated vinyl or fiber cement, can improve a home’s insulation, reducing energy consumption and lowering utility bills. These materials often incorporate insulation layers that help maintain a stable indoor temperature, minimizing the reliance on heating and cooling systems.
Conversely, some siding materials, like certain types of metal siding, might have lower insulation values, potentially leading to higher energy consumption if not properly insulated behind the siding. The energy efficiency of siding should be carefully considered, especially in climates with extreme temperatures, as it directly impacts a home’s overall environmental impact and operational costs.