How to properly prepare the wall before installing DIY siding? It’s more than just slapping up some new panels! This seemingly simple task actually involves a crucial series of steps that determine the longevity and aesthetic appeal of your project. From assessing the existing wall surface for damage and prepping it with a thorough cleaning to repairing imperfections and applying primer, we’ll guide you through every essential stage.
Get ready to transform your exterior with a DIY siding project that’s built to last.
This comprehensive guide breaks down the process into manageable steps, offering practical advice and solutions for common wall types – brick, wood, stucco, and concrete. We’ll cover everything from identifying and fixing cracks and holes to leveling uneven surfaces and applying the right primer and sealant for optimal results. Whether you’re a seasoned DIYer or a complete novice, this guide will empower you to tackle your wall preparation with confidence and achieve a professional-looking finish.
Assessing the Wall Surface
Preparing your wall for DIY siding is crucial for a long-lasting and aesthetically pleasing result. A thorough assessment of the existing wall surface is the first and most important step. Ignoring potential problems can lead to costly repairs down the line, compromising the structural integrity and visual appeal of your siding. This section details how to properly inspect your wall before beginning installation.
Wall Surface Types
Different wall materials require different preparation techniques. Understanding the type of wall you’re working with is paramount. Common wall surfaces include brick, wood, stucco, and concrete. Brick walls, often found in older homes, offer a strong and durable base, but require careful inspection for loose mortar. Imagine a classic red brick Victorian house; that’s a prime example.
Wood-framed walls, common in many modern homes, might be clad in plywood or other sheathing, necessitating checks for rot, warping, or insect damage. Think of a typical suburban home with its wood-framed structure. Stucco walls, known for their textured finish, need examination for cracks, loose sections, and water damage. Consider a Mediterranean-style home with its characteristic stucco exterior.
Concrete walls, typically found in more modern or commercial buildings, require an inspection for cracks, spalling (chipping or flaking), and efflorescence (salt deposits). Picture a sleek, contemporary building with smooth concrete walls.
Inspecting for Wall Damage
A meticulous inspection is key to identifying potential problems before they become major headaches. Begin by visually inspecting the entire wall surface from a safe distance, noting any obvious cracks, holes, loose mortar, or signs of water damage. Then, get closer and use your hands to feel for loose or unstable areas. Tap the wall gently with a hammer or other tool; a hollow sound might indicate rot or void behind the surface.
Pay close attention to areas prone to water damage, such as corners, around windows and doors, and low-lying sections. Examine caulking around windows and doors for cracks or gaps. Use a moisture meter to check for hidden water damage. Any discoloration or staining on the wall surface is a potential sign of water intrusion.
Wall Surface Problems and Repair Methods
Problem | Severity | Repair Method | Example |
---|---|---|---|
Small Cracks in Stucco | Low | Fill with high-quality caulk or patching compound. | Thin hairline cracks in stucco walls. |
Large Cracks in Concrete | High | Consult a structural engineer; may require significant repair or reinforcement. | Significant cracks extending across a concrete wall section. |
Loose Mortar in Brick | Medium | Repoint the mortar using a matching type. | Missing or crumbling mortar between bricks. |
Rotting Wood | High | Replace the affected wood; treat surrounding areas with a wood preservative. | Soft, spongy wood showing signs of decay. |
Water Damage Staining | Medium | Address the source of the leak; repair damaged areas and apply a waterproof sealant. | Dark stains or discoloration on the wall, particularly near window frames. |
Cleaning and Preparing the Wall

Getting your wall ready for DIY siding is crucial for a long-lasting, beautiful finish. A clean, properly prepared surface ensures the siding adheres correctly and prevents future problems like peeling or water damage. This means tackling dirt, debris, loose paint, and even mildew before you even think about picking up your first piece of siding.Cleaning the wall thoroughly is the first step in preparing it for new siding.
This involves removing all dirt, debris, loose paint, and any mildew growth. Failure to properly clean the surface can lead to adhesion problems and compromise the longevity of your siding installation.
Wall Cleaning Methods
Effective wall cleaning requires a multi-pronged approach. Begin by using a stiff-bristled brush to remove loose dirt, dust, cobwebs, and any other surface debris. For stubborn dirt, a pressure washer can be incredibly effective, but use caution to avoid damaging the underlying wall material. Always start with a lower pressure setting and test a small, inconspicuous area first.
For mildew, a solution of one part bleach to three parts water applied with a scrub brush is usually sufficient. Allow the solution to sit for several minutes before scrubbing and rinsing thoroughly with clean water. Remember to wear appropriate safety gear, including gloves and eye protection, when working with bleach. For heavily soiled areas or areas with significant mildew growth, consider using a commercial-grade cleaning solution specifically designed for exterior surfaces.
Always follow the manufacturer’s instructions carefully.
Drying the Wall Surface
After cleaning, allowing the wall to completely dry is paramount. Dampness trapped beneath the siding can lead to mold growth, rot, and ultimately, siding failure. The drying time will depend on factors like weather conditions, wall material, and the amount of moisture present. In ideal conditions, a few hours of direct sunlight might suffice, but it’s better to err on the side of caution.
Proper wall prep is key for a long-lasting DIY siding project; you wouldn’t want to waste time and effort on a subpar base! Choosing the right siding material significantly impacts your project’s longevity, so check out this article comparing the lifespan of various siding options: comparing the lifespan of various siding options to make an informed decision.
Remember, a smooth, clean, and properly primed surface ensures your siding adheres correctly and maximizes its lifespan, regardless of the material you choose.
Allow at least 24 hours for the wall to dry completely before proceeding. You can check for dryness by pressing a clean, dry cloth against the wall; if no moisture transfers to the cloth, the wall is likely dry enough. In humid conditions or for porous materials, you may need to extend the drying time even further.
Using fans to circulate air can help accelerate the drying process.
Removing Old Siding or Paint
Removing existing siding or paint is often necessary before installing new siding. Several methods exist, each with its advantages and disadvantages. Scraping is a relatively simple method for removing loose paint or old siding, using a scraper or putty knife. However, it can be labor-intensive and may not be effective for stubborn paint or heavily adhered materials. Sanding can smooth surfaces and remove minor imperfections but is also time-consuming and generates dust.
Proper DIY siding installation starts with a meticulously prepared wall. Before you even think about attaching the first panel, thoroughly inspect for any damage, ensuring the surface is clean and dry. Addressing pest infestations is crucial; if you find evidence of insect damage, check out this helpful guide on dealing with siding issues caused by pests and insects before proceeding.
Failing to do so could compromise the longevity of your new siding, so proper wall prep is key for a successful DIY project.
Chemical stripping uses specialized paint removers to soften and loosen paint, making it easier to scrape off. This method is effective for tough paint but requires careful handling due to the chemical nature of the removers. Always wear appropriate safety gear and follow the manufacturer’s instructions when using chemical strippers. The best method depends on the type and condition of the existing siding or paint.
For instance, if you are dealing with lead-based paint, you should contact a professional for removal to avoid health hazards.
Repairing Wall Imperfections: How To Properly Prepare The Wall Before Installing DIY Siding
A perfectly smooth wall is crucial for achieving a professional-looking DIY siding installation. Before you even think about attaching your new siding, you need to address any imperfections on the wall itself. Ignoring cracks, holes, or uneven surfaces will lead to an uneven finish and potentially compromise the longevity of your siding. This section will guide you through the process of repairing common wall imperfections.
Patching Cracks and Holes
Repairing cracks and holes requires the right materials and a steady hand. Common fillers include spackling paste for smaller imperfections and patching compounds for larger holes. For a common-sized hole, say about the size of a golf ball, follow these steps:
- Clean the area thoroughly, removing any loose debris or dust. A wire brush can be helpful for stubborn dirt.
- Use a putty knife to apply a generous amount of patching compound, slightly overfilling the hole. Press firmly to ensure good adhesion.
- Allow the compound to dry completely according to the manufacturer’s instructions. This usually takes several hours.
- Once dry, use a sanding block or sandpaper to smooth the patched area flush with the wall. Start with coarser grit sandpaper and gradually move to finer grit for a smoother finish.
- Prime the patched area before applying paint to ensure proper adhesion and prevent discoloration.
Addressing Water Damage
Water damage is a serious issue that needs immediate attention. The first step is identifying the source of the leak. Check for damaged roofing, faulty gutters, or cracks in the exterior walls. Addressing the source of the leak is crucial to prevent further damage. Once the leak is fixed, you can move on to repairing the affected area.
Sealing cracks is critical in preventing future water intrusion. Use a high-quality exterior-grade caulk to fill any cracks or gaps. Ensure the caulk is compatible with the wall material. For larger areas of water damage, you may need to replace damaged sections of drywall or other wall materials.
Leveling Uneven Wall Surfaces
Uneven walls are a common problem, especially in older homes. Leveling these surfaces is essential for a professional-looking siding job. For minor imperfections, you can use a skim coat of joint compound applied with a wide putty knife. Imagine applying a thin layer of mud, smoothing it out in long, even strokes to create a consistent surface.
For more significant unevenness, consider using drywall shims or furring strips to build up the wall surface to a uniform plane. Visualize this as building small platforms along the wall’s surface, creating a level foundation for the siding. Once the shims or furring strips are in place, you’ll need to cover them with drywall or another suitable material before applying the skim coat.
The result will be a uniformly flat wall surface, ready for siding installation.
Priming and Sealing the Wall
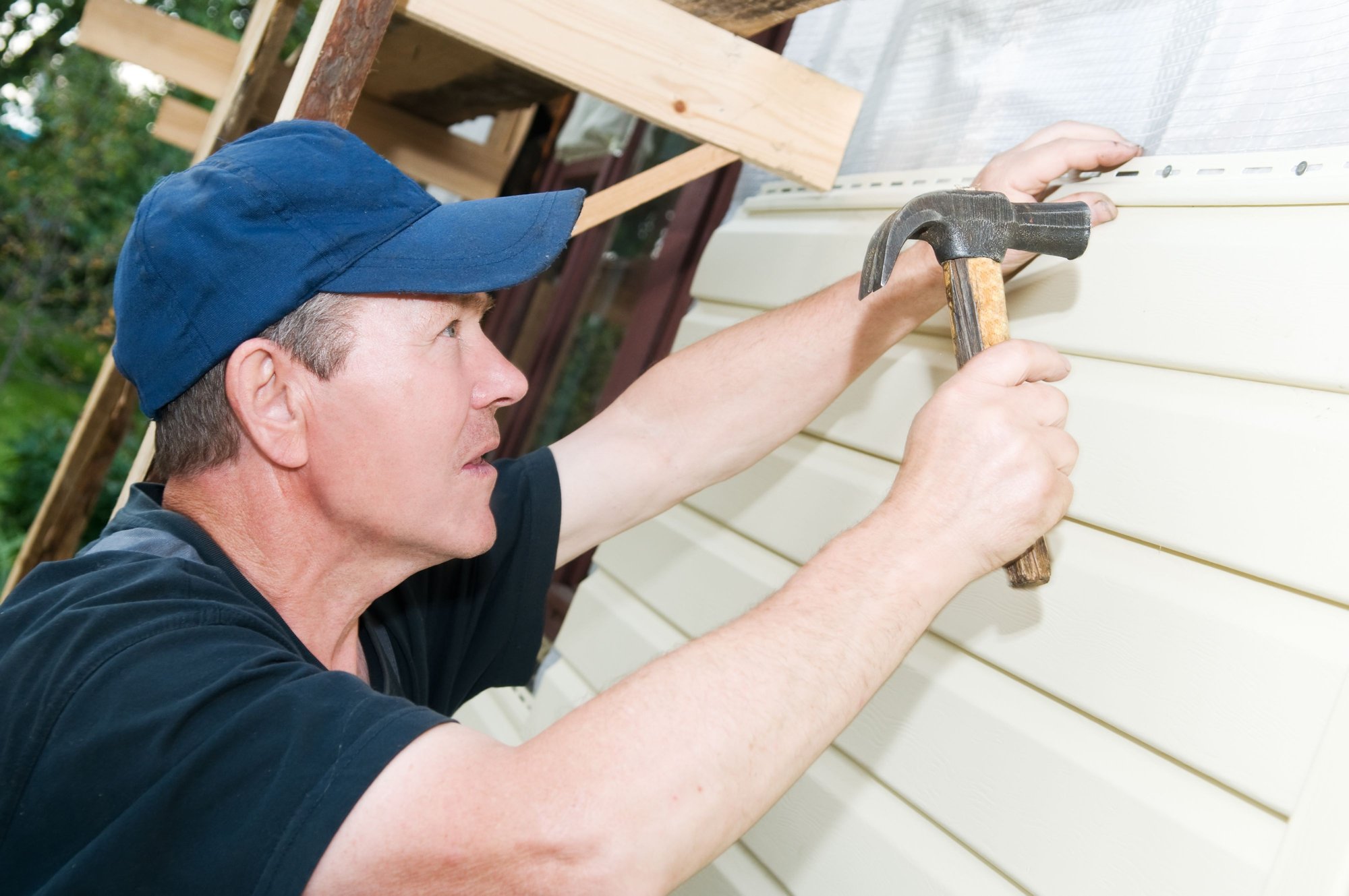
Preparing your wall for DIY siding involves more than just patching holes. A crucial step often overlooked is priming and sealing, which significantly impacts the longevity and aesthetic appeal of your final project. Proper priming provides a consistent surface for the siding to adhere to, while sealing protects the wall from moisture damage, ensuring a long-lasting, beautiful finish.Priming the wall creates a uniform surface for the siding to adhere to, improving the bond and preventing issues like peeling or bubbling.
Different primers are suited to various wall materials, offering specific benefits. For instance, oil-based primers penetrate deeply into porous surfaces like wood, providing excellent adhesion and stain blocking. Conversely, acrylic primers are ideal for smooth surfaces like concrete or brick, offering good adhesion and quick drying times. Choosing the correct primer is key to a successful installation.
Primer Application Techniques
Applying primer evenly is crucial for a professional finish. Begin by stirring the primer thoroughly to ensure consistent viscosity. Use a high-quality roller for large areas and a brush for corners and edges. Work in manageable sections, applying thin, even coats to avoid drips and runs. Allow each coat to dry completely before applying the next, following the manufacturer’s instructions.
In hot, sunny conditions, work in the shade or during cooler parts of the day to prevent the primer from drying too quickly. Conversely, in cold or damp weather, ensure adequate ventilation and allow for extended drying times. Multiple thin coats are always preferable to one thick coat, which is more prone to cracking and peeling.
Sealant Application and Selection
In areas prone to moisture, such as bathrooms or basements, applying a sealant or waterproofer is essential to prevent water damage and mold growth. Several sealant types exist, each with its specific application. Acrylic sealants are versatile, offering good adhesion and flexibility, making them suitable for most exterior applications. Silicone sealants provide excellent water resistance and are ideal for areas with high moisture exposure.
For instance, using a silicone sealant around windows and doors will help prevent water infiltration. Always follow the manufacturer’s instructions regarding application and drying time. For optimal results, apply a thin, even bead of sealant, smoothing it out with a damp finger or smoothing tool. Avoid over-application, as this can lead to cracking and peeling.
Installing Furring Strips (if necessary)
Furring strips are thin pieces of wood, typically 1×2 or 1×3 inches, used to create a level and consistent surface for installing siding. They’re essential when your existing wall isn’t perfectly flat or plumb, or if you need to add extra space for insulation or ventilation. Using furring strips provides a superior base for your siding, ensuring a professional-looking and long-lasting finish.
Without them, uneven walls can lead to gaps, crooked siding, and potential damage to the underlying structure.
Furring Strip Selection and Measurement, How to properly prepare the wall before installing DIY siding
Choosing the right furring strips depends on your wall’s condition and the type of siding you’re installing. For most DIY projects, standard 1×2 or 1×3 inch lumber is sufficient. Measure the wall’s height and width to determine the number of strips needed. Remember to account for any obstructions or irregularities. Cut the strips to the appropriate length using a miter saw or hand saw, ensuring clean, straight cuts for optimal installation.
Pre-drilling pilot holes before fastening will prevent the wood from splitting.
Furring Strip Installation
Installing furring strips involves a straightforward process. Begin by establishing a baseline using a level and a chalk line. This will guide the placement of your first strip. Use appropriate fasteners for your wall material; for example, masonry anchors for brick or concrete, and construction adhesive and screws for wood or drywall. Space the furring strips evenly, usually 16 to 24 inches apart, depending on the siding material and manufacturer’s recommendations.
For added stability, consider staggering the seams of adjacent strips. When working with brick or concrete, ensure the masonry anchors are appropriately sized and securely installed. For wood or drywall, pre-drilling pilot holes is crucial to prevent the wood from splitting, and construction adhesive enhances the bond for better stability.
Ensuring Level and Plumb Installation
Maintaining level and plumb furring strips is crucial for a professional finish. Use a level to check the horizontal alignment of each strip before fastening. A plumb bob or laser level can assist in verifying vertical alignment, especially for taller walls. Make adjustments as needed using shims or by slightly repositioning the strips. Remember to regularly check the level and plumb throughout the installation process to catch any inconsistencies early on.
Regularly checking your work with a level and plumb bob will ensure a smooth, even surface for your siding installation. This meticulous approach guarantees a professional-looking finish, preventing issues like gaps or crooked siding.